A coalescer, also known as a coalescing filter, is a device that uses the coalescence principle to separate fluid mixtures into different fluids. In the process of coalescence, molecules of the same fluid clump together to form a larger fluid unit. Similar to particulate filters, coalescing filters are used to separate the particulate components of mixtures- in this situation, mixtures of liquids. Read More…
Our company is the filtering systems expert. We know everything there is to know about filtering liquids and oils for many industries ranging from the petrochemical industry to waste water management. It is our goal to provide customized solutions that you can trust and rely on every day. You will find that our attention to detail and superior service can help you in multiple ways. Contact us to...

Hydraulic filtering systems are used in construction machinery, agricultural machinery and mechanical handling. MPI Filtri has more than 40 years of experience in filtering systems and industrial filtration. We offer suction filters, return filters, pressure filters and spin-on filters.
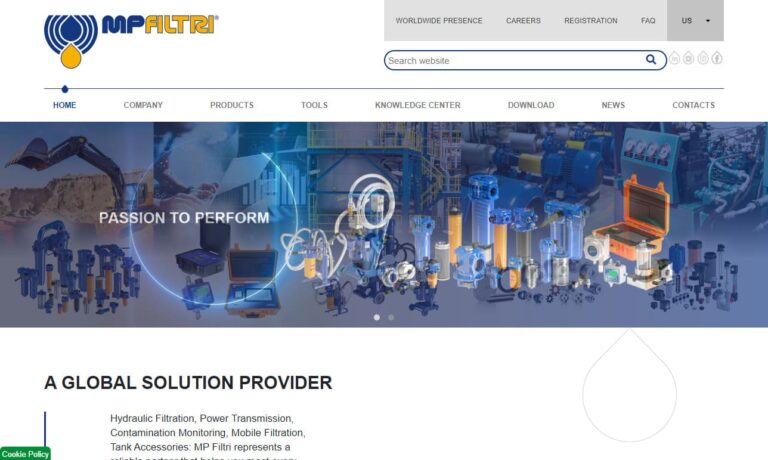
We have been at our present factory location for over twenty years and are recognized as one of the prime producers of anthracite media in the world. We produce nearly 300 specifications of Anthrafilt, most between .60 and 1.80mm.
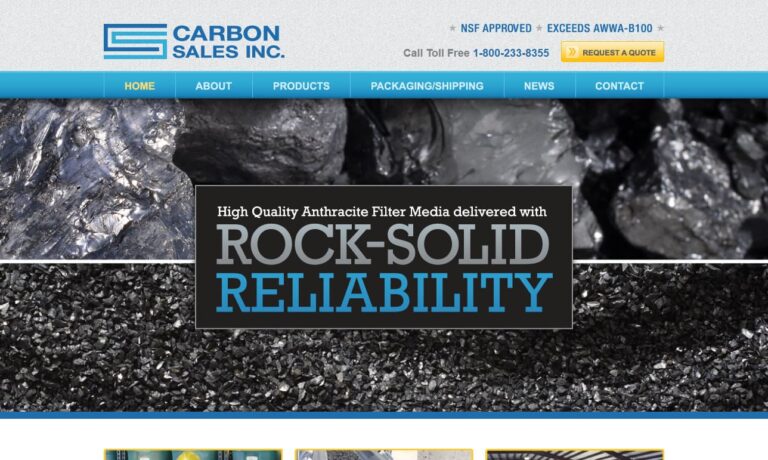
Filtertech is an international producer of liquid filtration and waste disposal systems for industrial coolant applications including wire drawing, aluminum and steel rolling, machining, grinding, process water applications such as CV water, caster water, vibratory applications and optical lens generating. Filtertech provides complete turnkey filtration and waste treatment systems utilizing its...
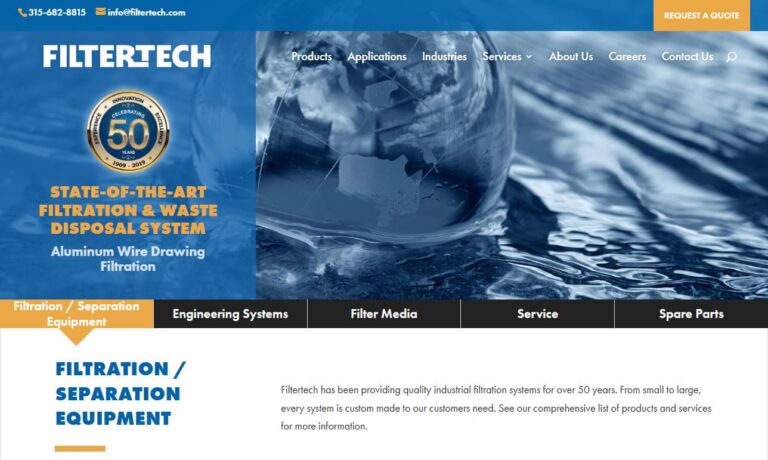
PurAqua is a leader in water cleanliness products for industrial applications and commercial pools. If you are looking for chemical feed systems (Accu-Tab / PPG), controllers (Chemtrol / CAL) or filtering systems, you came to the right place. PurAqua Products is proud to be a leading supplier of commercial chlorinator and aquatics pool replacements parts. For commercial pool feed systems, parts...
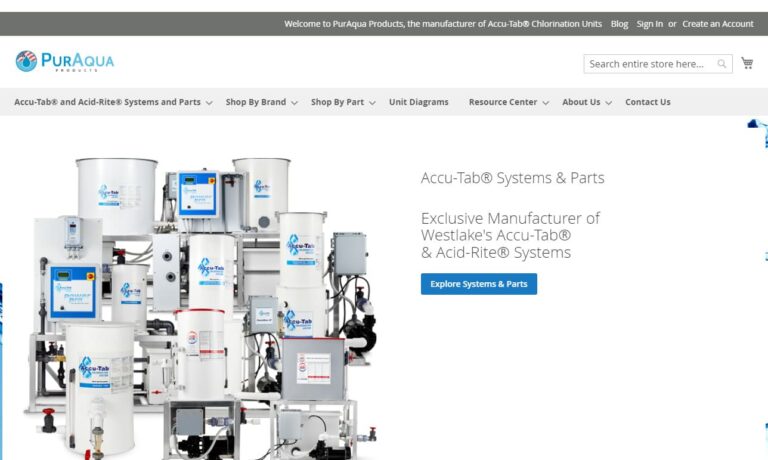
More Coalescing Filter Manufacturers

Coalescers can be used independently or as parts of larger separation units. The appropriate type of coalescing filter must be chosen based on the characteristics of the substances to be separated. For instance, a gas coalescer is used to extract gasses from gas-fuel or gas-water emulsions, whereas an oil coalescer or fuel coalescer can be used to recover oil or fuel from a water-oil mix, respectively.
How Coalescing Filters Work
A coalescing filter is a filtration system made up of several baffle walls or screens. The filter receives a stream of fluid that needs to be separated (such as a gas-water mixture), and the baffles separate the various components by trapping them in distinct areas based on their weight and density. Once the undesired, polluting fluid is drained away for purification or disposal, the desired fluid can be recovered in its original state.
The screening mechanism of a coalescing filter operates based on the physical characteristics of the different fluids, such as molecular weight and density. While a liquid’s vapor molecules diffuse through the filter element to coalesce and be drained out of the system gravitationally, the molecules of the undesired fluid are diverted in one direction to a drain point by the baffle walls in the coalescing filter.

In a similar way, "wet gas" (gas stream containing water droplets) is fed into the coalescer inlet, diffuses through a filter element, and departs via an output port as dehydrated gas in gas-water separation. For drainage, the denser fluid’s molecules agglomerate and sink to the tank's bottom. The removed fluid is discarded in some applications after it is collected and recycled when it is a valuable liquid.
A coalescing filter may employ a third layer when precious oils or aerosols need to be collected. In these instances an inner layer made of very fine material is set between the two outer layers to ensure that the resulting coalesced material is further purified. Regardless of the number of layers, the fibrous materials that make up coalescing filter panels or cartridges form a sophisticated matrix or lattice. Examples include fiberglass, closed-cell foam, borosilicate microglass, and other long-lasting and chemically-resistant latticed materials.
Types of Coalescing Filters
Mechanical Coalescing Filters
Mechanical coalescing uses a number of barriers, or filter elements, for separation. The production of coalescing filter elements frequently uses membrane technology and borosilicate (boron and silicates) microfibers. The selection of specific filter elements determine how pure the final products are after separation. Mechanical coalescers are employed in oil refineries to separate water vapor from hydrocarbon condensate by coalescing the water molecules into larger particles that are then drained out of the system.

Electrostatic Coalescing Filters
Electrostatic coalescing filters use an AC (alternating current), DC (direct current), or a combination of both currents to cause droplet coalescence in fluid mixes. By applying an electric charge to the fluid, electrostatic coalescers destabilize the emulsion and enlarge the molecules, forcing them to fall into a collection tank for drainage.

For this reason, AC currents in the 50–60 Hz (Hertz- a unit used to measure sound waves) range are typically employed. Fluid molecules condense to form heavier molecules as a result of the forces of attraction created by a produced electric field. Electrostatic coalescers are frequently used for separating water-fuel emulsions in offshore oil and gas production facilities.
Benefits of Using Coalescers
Coalescers used in microfiltration provide products with up to 95% purity. Additionally, they are environmentally benign and use a lot less electricity than other industrial filtration techniques.
Applications of Coalescing Filters
Coalescers are used in the oil and gas industry for product refinement. Coalescing filters are employed at natural gas refineries to dehumidify natural gas and guarantee product purity before selling this product. Aerosols, particulate matter, dissolved hydrocarbon liquids, and sludges are just a few of the fluids that are pumped into the compressor inlet and are removed by a coalescing filter.Systems that use gas-oil coalescers can clean natural gas by removing condensate and a number of natural liquids.
Additionally, by removing impurities like water vapor and sulfur with efficiency as high as 99.98%, coalescing filters are actively utilized to avoid corrosion in downstream oil and gas assets like compressors, amine/glycol absorbers, turbines, and membrane filtration systems. When positioned at a compressor's outlet, coalescing filters can be used to collect lubricating oil from the device.
Prior to storage of gas, water vapor, amine solutions, and sulfur can be phase-removed from petrochemical feedstock using liquid-liquid coalescers. This process not only ensures product purity, it also stops industrial equipment from corroding.
Choosing the Proper Coalescing Filter Manufacturer
To make sure you have the most productive outcome when purchasing a coalescing filter from a coalescing filter manufacturer, it is important to compare several companies using our directory of coalescing filter manufacturers. Each coalescing filter manufacturer has a business profile page highlighting their areas of experience and capabilities, along with a contact form to directly communicate with the manufacturer for more information or request a quote. Review each coalescing filter business website using our proprietary website previewer to quickly learn what each business specializes in. Then, use our simple RFQ form to contact multiple coalescing filter companies with the same form.